CTT Improves Strict SLA Compliance With Fluorescent UPU Mail Code Scanning
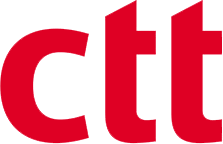
Key Results
- Scans fluoro barcodes in under 1 second and read rate above 98%
- Reduced risk of SLA breaches and compliance-related penalties
- Increased audit sample size from 500 items per month to 80,000 per month
Integrations
Geography
PortugalIndustry
Post, Parcel and ExpressUse Case
Proof of Delivery
With more than 500 years of history, CTT is Portugal’s first and oldest mail provider. The company is responsible for sorting, distributing, and delivering more than 1.5 million items each day across Iberia (Portugal and Spain), equating to more than 400 million items per year.
Whilst delivering this volume of items, CTT must adhere to one of the European Union’s (EU) strictest mail delivery service level agreements (SLA). The ability to accurately track mail delivery timelines is essential for CTT to avoid the risk of huge financial penalties.
CTT integrated the Scandit Barcode Scanner SDK into its last mile mobility app, MOBI, with a first-of-its-kind ability to scan fluorescent barcodes on smart devices (previously only scannable on specialist sorting machines), to improve mail delivery visibility, enrich its data samples, and ensure compliance with the SLAs.
“Our project goals were to get the fluorescent barcode read speed under one second and the average read rate at above 98% for our mail carriers. Both were met without any problems, we’re very happy with the Scandit solution.”
Jorge Raminhos, Head of Operations, Technology, Mobility and Sustainability – CTT
Challenge
CTT is governed by one of the strictest mail SLAs in the entire EU, regarding the Universal Service Obligation (USO) which demands a quality of service that mail and telecommunications companies must meet. CTT also places great importance on providing its many customers with a positive experience; customer focus, proximity, and confidence are all core values of the CTT Group.
Scandit has been partnered with CTT since 2020, providing barcode scanning and smart data capture to support its last mile delivery and postal operations.
The company is audited each year to test the quality of its services. Part of this process is to send fictitious ‘dummy’ letters to track if delivery time SLAs are met. Failure to comply or reach the SLA can result in huge fines or requirements to make large financial investments to improve the service.
In order to avoid such penalties, and to ensure customer satisfaction, CTT recognized the need for a more accurate way of tracking mail deliveries. This meant finding a solution that could improve data capture across the mail delivery process.
However, the fluorescent barcodes on mail have historically only been readable by specialized fixed machines using ultraviolet light. To update these machines with printers that would add codes that are readable by other devices would be expensive and extremely disruptive.
The key question was: how could CTT effectively read the fluoro codes in the field without incurring huge hardware costs?
Jorge Raminhos, CTT’s Head of Operations, Technology, Mobility and Sustainability explains: “The major challenge that we had was that without these quality of service metrics, we were not sure about the satisfaction of our customers, which is very important to CTT. We were also concerned about the big fines that can be imposed when we don’t meet the SLAs that are defined by our regulator in Portugal.”
CTT uses specific high-throughput printer-scanners that use the UPU S18 4-State Barcode symbology, a standard used by postal operators for mail sorting. However, field devices have so far been unable to scan the fluorescent codes for tracing purposes.
Raminhos comments: “We tried several scenarios. One of them was to add a new printer for each sorting machine, but this wasn’t ideal”.
This would have meant printing an additional barcode in black ink to each mail item during the sorting process, something that Raminhos says would have been prohibitive because of the long implementation timeline, and because the total cost of ownership (TCO) would have been “very high”.
CTT felt the answer lay in the fluorescent mail codes printed onto envelopes and flat parcels during the sorting process. But the challenge remained: how to capture and track fluorescent orange barcodes on more than 40,000 letters that are printed per hour using mobile devices?
Solution
The solution had to be able to scan the code on any smart device carried by more than 5,000 CTT mail delivery workers – something that had never been done before outside of the static sorting machine.
Having invited several potential partners to take on the challenge, only Scandit was able to deliver a working solution for testing – and did so quickly.
Jorge Raminhos says: “The process was very quick. The approach was made with Scandit in the beginning of the summer, and then by September, we had the fluoro scanning solution implemented. We conducted some tests and the solution met all of the demanding criteria that we had”.
Those criteria centered around the scanning performance of the solution; CTT required a product that scanned quickly and accurately.
“Both criteria were met and the solution was perfect. The team was awesome”, Raminhos says.
The Scandit solution was integrated with the CTT MOBI app, used by its mail delivery employees in the field via smart devices.
During the mail sorting process, CTT added two digits to each fluorescent barcode to indicate the SLA delivery timeframe. The company tracks the data collected from the scans via a custom reporting dashboard, which helps to monitor performance.
Results
From a performance perspective, the Scandit solution exceeds CTT’s targets for the fluorescent barcodes, providing:
- Scans in under 1 second
- A read rate of more than 98%
Raminhos comments: “The criteria was met without any problems. We are very satisfied with the solution.”
Furthermore, for regular single barcode scanning in the depot (used when scanning manifest lists), CTT has reached:
- 0% false positives
- A more than 99.99% scan rate
Larger, more reliable sample size reduces compliance risks
CTT’s previous audit process used samples of around 500 mail objects per month. Since implementing the Scandit solution, CTT has drastically increased this number to around 80,000 per month. The sample is completely random and not based on fictitious objects created specifically for the audit process.
This provides a much larger and more reliable sample size, and CTT anticipates no compliance-related issues, helping it to avoid SLA-related penalties, and in turn allowing increased customer satisfaction.
Improved data quality, visibility and value
The improved data collection has led to better visibility of service quality metrics and performance across the CTT postal operation. Dashboards and daily indicators allow for better control and process tuning. This data powers an enriched tracking system that records delivery times, providing high value to CTT and allowing the company to continuously improve performance.
Richer data also presents opportunities for future initiatives, such as mail route optimization. According to Raminhos, the information gathered will provide knowledge about the specific routes taken by the mail workers:
“This is also the foundation solution for a key problem that we have. For instance, in the summer, in Algarve and in other regions, the toponymy is poor and we must depend on the knowledge of the mail workers to plan the route”, he says.
Low disruption and easy adoption
A key benefit of the Scandit solution is its ease of adoption within the daily workflows of CTT’s postal workers. Because the sample collection occurs almost naturally in the daily work of the delivery people, via the smart devices they already carry, the scanning process has had next to no intrusive impact on the delivery process.
Jorge Raminhos says of the Scandit integration: “It was the full solution that we were searching for, without any intrusive new processes, without any new code, and without any disruption in the last mile. We need the mail workers to deliver the objects and not to spend more time processing. Of course, they need to read the barcodes, but the process is very simple and they don’t need to spend too much time doing it”.